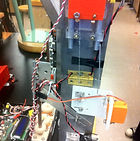
3D parts
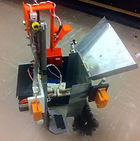
Walls
Stack City's mechanical components were designed on Solidworks and made on either the 3-D printer, the water jet, using hand tools or a combination of the three.
Mechanical design
The main components of the robot was the two steel arms. These arms were cut using a waterjet and bent to shape. The mounts that the two arms stand on were also cut using the water jet along with the gears, shovel and any other metal piece on the robot.
Many 3-D parts were used to make this robot. All servos were constructed out of 3D printed parts, the wheel rims, the pully and mounts for the shovel and push button coverings.
The servos on Stack City were held in place by 3D printed mounts. The two on the walls were constructed to hold the servos parallel to the wall and the ones in the chassis were constructed to hold the sevo vertically upwards. These chassis servos allowed the walls to be moved and were mounted to gears to provide a more stable attachment and a larger angle of rotation.
In order to gain traction on the course, many different materials were tested. In the end, it was found that orange wire insulation, on 3D printed wheels provided the best traction. These wheels were attached to geared motors to allow the robot to move. The front of the robot had ball bearings, with a 3D printed casing to hold them in place. This allowed our robot to make the sharp 90 degree turns that was required in the competition.
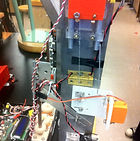
Servos

Wheels